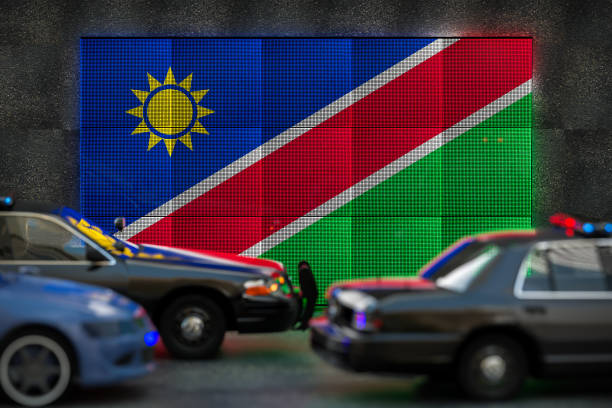
In South Africa, the local operations of multinational motor manufacturing companies are constantly developing to meet the demands of global markets and deliver an advantage in the marketplace. The method of work is constantly changing.
The technology currently being used at work are more sophisticated than the technologies that existed before.
Fueled by economic factors, this development only sometimes leads to social changes. Combined with modern working methods and technology, automation and robotics in manufacturing may create adverse social effects on workers.
Job Automation in South Africa
There has been a rise in technology within South Africa’s automotive industry since 2003. Most of the work in the manufacturing of vehicles is now automated, making production quicker, easier, and more efficient. A more significant number of vehicles are made every day. The companies used to produce just 20 units of vehicles every hour. Today, they produce over 100 units in an hour, using the same amount of autoworkers.
Our research of the sector revealed that automation technology is advanced. The body shop of the sector is entirely automated. Paint shops are 100% automated. The paint shop has about 20% utilization of technology in the auto assembly line. Logistics has increased the use of machines than it did before.
These figures indicate how workers need to catch up in the battle with technology in the workplace. Many workers feel demotivated and need help to fully utilize their talents to complete their jobs as robots take over most tasks. Others are being transferred to assembly lines, expected to become automated with time. The increase in automation of jobs and the degrading of skills could lead some people to leave their job as machines replace their skills.
We gathered information through deep interviews with 30 people from three automotive firms. The participants included autoworkers, managers, and representatives of workers.
Interviews with management have revealed that management does not necessarily favor machines over human employees. However, to be competitive, it must be able to consider production capacity, quality, and economics of the workplace.
When they plan to use machines, it has not intended to replace workers’ work but to accomplish specific tasks that require using machines. For instance, one cannot expect people to lift a car when another person is working under it. The machine could do it without putting the workers at risk. However, management has stated that if given the opportunity, they would replace workers with robots since they can perform more efficiently and increase productivity without negotiations.
What does automation mean for employees?
While robots have helped ease the work process, their increased usage slows the workforce on the shop floor, body shop, paint floor, and assembly line.
The choices that led to the relocation of many autoworkers from the paint and body shops to join the production line are irreversible. One worker told me:
If you were to look at the old press line, it would have a minimum of 20 workers. Today, you need only four workers to load the components. Thus, the number of workers is reduced by introducing five robots. The affected workers are transferred to different areas within the company at present.
The automobile industry’s growth is not a source of employment for humans. When automation does create jobs, it is mainly in the management of technology. It does not create work for people with existing skills.
This is a risk of a growing rate of unemployment, which was 30.1 percent in the initial quarter of 2020. This, in turn, is a factor in South Africa’s standing as one of the most unjust nations in the world.
Driving forces
Technology adoption can free workers from the burden of jobs and increase productivity, but they will also likely eliminate workers from their jobs.
To increase efficiency and reduce cost, the global auto industry anticipates thousands of job reductions, with estimates of 234 000 job losses until 2030 in Germany as well as 12 000 job reductions through Ford in Europe before 2020 and a loss of 2 000 jobs in India at the end of 2020.
In our study, we found that the capability of the workers’ union that is the National Union of Metalworkers of South Africa, to work together to reform the auto industry together with management and improve the lives of all stakeholders is diminished because of the coercive control of management and the top-down union arrangement.
Innovation is the primary driver of consumers, which is what management does, too. However, instead of prioritizing innovation over all other things, industrial policymakers must seriously consider how it could enhance the human condition before it causes problems by contributing to the loss of jobs, job uncertainty Deskilling, inequality, and job loss.
The solution would be to preserve current jobs, create more opportunities for work, revamp the industrial policies, decrease the proportion of tasks assigned to technology, and make the automotive manufacturing process more labor intense than capital-intensive.
The state, the car industry, and unions, workers’ society as a whole all have a part in bringing about significant changes in the economy and reforms to employment that is sustainable for everyone.